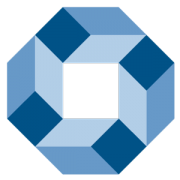
White & Partners has sponsored a new state of the art off-site modular manufacturing business called Bedrock Offsite, located in the northern suburbs of Sydney. Bedrock manufactures fully completed bathroom, kitchen and laundry modules for residential, aged care, student accommodation and hotels.
White & Partners is observing throughout the construction and development industry widespread cost, delivery and risk pressures. Prefabricated construction completed ‘off-site’ in a controlled factory environment, and installed on-site, provides a significant step towards addressing these challenges. This solution is ideally suited to large scale projects.
What’s interesting is that this technology is by no means new. Prefabricated construction makes up 70% of the total construction spend in Sweden, 50% in Japan and 30% in the UK; however it makes up just 3% in Australia. Despite being late adopters, interest in Australia is now increasing exponentially.
Many construction risks are mitigated. It is quicker, cheaper, and safer, less waste, more sustainable and superior quality.
Some ways prefab can improve the construction process:
Ideally in order to maximise the opportunity, developers and builders need to contemplate and engage in the incorporation of modular manufactured solutions in the DESIGN stage of projects. For more information or a tour of our facilities please contact David Michel at Bedrock Offsite on 0408 865 717.